

Parker's Domnick Hunter filtration division is the global leader in gas generation and filtration having the he most complete product line of Air Treatment and Nitrogen Generators, Desiccant Dryers, Refrigerated Dryers, Biogas Filtration and Chillers.
Unleash Peak Efficiency with the NITROSource Plus PSA Nitrogen Gas Generator Range!
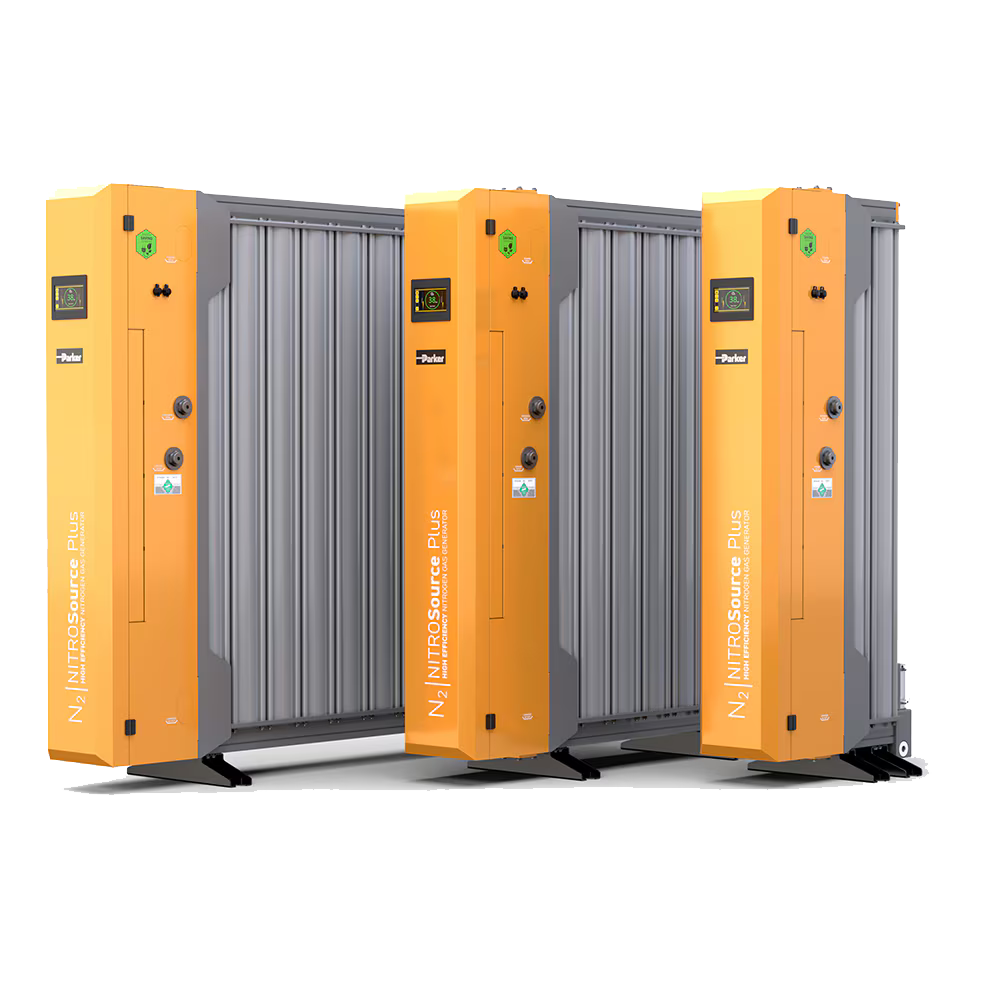
Experience unparalleled performance and operational excellence with the cutting-edge NITROSource Plus PSA nitrogen gas generators. Engineered for maximum efficiency, this innovative range delivers reliable, high-quality nitrogen to power your operations like never before.
Advanced Oxygen Analysis: All models feature an integral Zirconia oxygen analyzer for precise and rapid monitoring with extended service life. For pharmaceutical compliance, an optional electrochemical oxygen analyzer aligns with European Pharmacopoeia standards.
Safety Assurance with Off-Gas Bypass: If oxygen levels exceed specifications, the generator automatically vents out-of-spec gas and purges to restore purity, preventing contamination.
Stable Flow Control: A mass flow controller ensures consistent nitrogen flow and pressure, safeguarding the CMS bed from overloading and maintaining gas purity, even during downstream fluctuations.
Energy Saving Technology (EST): Optimizes cycle timing based on oxygen monitoring, reducing compressed air usage under part-load conditions for greater efficiency.
Pressure Regulation: Outlet pressure regulation ensures stable nitrogen supply, protecting processes from pressure fluctuations and overloading.
Parker’s PCO2 System: Safeguarding In-Plant Carbon Dioxide Quality for Industry Compliance

This Parker protection system is a comprehensive solution that preserves and guarantees the quality of the gaseous CO2 used in bottling of sparking beverages, preventing accidental contamination during the process. Utilizing advanced multi-layer adsorbent technology, the PCO2 range effectively accommodates flow rates from 181 to 4,354 kg/h at 24 bar g (400 to 9,600 lb/h at 350 psi g), ensuring optimal plant-scale protection. Functioning as a critical safeguard against quality incidents, this system efficiently eliminates a broad spectrum of potential carbon dioxide impurities. By maintaining gas quality in accordance with industry and company standards, it helps avert negative impacts on the final beverage, protecting both the producer's reputation and their bottom line. Endorsed and recommended by leading global brands, the Parker PCO2 is the preferred choice in the beverage industry, with installations across over 150 countries worldwide. Features: Failure to treat contaminants in compressed-air systems can lead to corrosion, blockage, damaged equipment, premature desiccant changes, or product contamination. This results in inefficient processes, spoiled products, low efficiency, and higher manufacturing expenses. Contaminants like particulate, oil, micro-organisms, and exhaust can cause an unhealthy, unsafe work environment too. Compressed-air purification requires uncompromising performance and reliability, plus the right balance of air quality with low operational cost.
• Comprehensive six-stage filtration technology
• Maximum cartridge life of 12 months*
• Low maintenance requirements
• Integrated safety features for enhanced reliability
• Simple installation with a compact design
• Materials of construction independently verified to comply with FDA Title 21 Code of Federal Regulations
• Adherence to global compliance and legislation standards
*12-month operational life is dependent on certified beverage/ISBT grade CO2 usage and the presence of a mass flow meter.
Benefits:
• Guaranteed carbon dioxide quality—effectively removes a wide range of potential impurities and contaminants
• Reduced total cost of ownership
• Protection against impurities that can cause flavor defects, minimizing product spoilage and safeguarding • bottlers’ reputations
• Ensures carbon dioxide meets both industry and company specifications—restores 'out of specification' gas to within beverage quality guidelines
• International sales and service support backed by over 20 years of experience
Clearing Compressed Air for Industrial Excellence
The Parker domnick hunter’s OIL-X coalescing filters use four, to guarantee high-performance liquid removal. In one method, a high-efficiency drainage layer offers more fluid drainage, better chemical compatibility, and higher operational temperatures than ordinary material does. In another, the OIL-X design wraps the drainage layer under the lower end cap to remove coalesced fluid from the air-flow path, which boosts liquid-removal efficiency and offers more usable filtration surface area. Other methods involve surface tension breakers and drainage ribs cast into the filter bowl.